DISC FINISHING UNITS– CF STANDARD SERIES
The CF series of disc finishing machines can be used for any application that requires a perfect surface finish to be achieved in a very short time for a variety of workpieces such as in cutting, turning, milling and stamping tools, jewelry, etc. Disc finishing machines are modular in design and available as standard with 1 – 4 process drums. All controls are accessible from the front and clearly laid out. Many years of experience have gone into the development of these machines, which is why they are so popular with our customers.
- Very easy to operate :Speed, processing time, water/compound concentration, rinse cycles and all other main processes parameters can easily be set by means of the user-friendly Siemens touch screen control panel and up 75 different procssing programs can be stored.
- Absolutely reliable : The use of only top-quality materials and components throughout ensures trouble-free operation and a long service life.
- Extremely cost-effective : Comparatively low capital investment and a high potential for cost savings make the CF series excellent value for money.
- Perfect results : Deburring, smoothing, grinding and polishing – the entire range of applcations with just one machine.
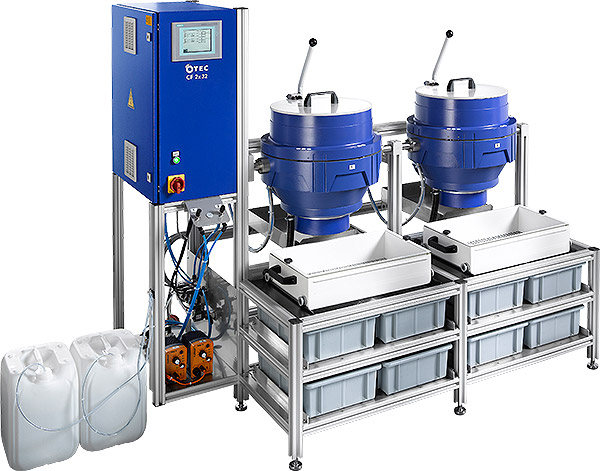
CF STANDARD SERIES
Disc finishing machines are modular in design and are available as standard with 1-4 process drums. The unique, patented gap system of the CF machines enables the gap to be set with an accuracy of 0.05 mm for dry finishing. The chassis is made of anodized aluminium profile and is therefore expecially resistant to corrosion and can easily be adapted to accept add-on equipment. All controls are accessible from the front and clearly laid out. Many years of experience has been channelled into these machines, making them very popular with customers.
STANDARD EQUIPMENT
- Process drums with hot moulded PU lining
- Aluminium profile chassis – easy to add on optional equipment
- Speed control via frequency inverter
- PLC touch screen control unit / 2D control unit (for the jewelry industry) with digital display of processing time, speed, rinse cycle, dosing and other key process parameters and storage for up to 75 different finishing programs.
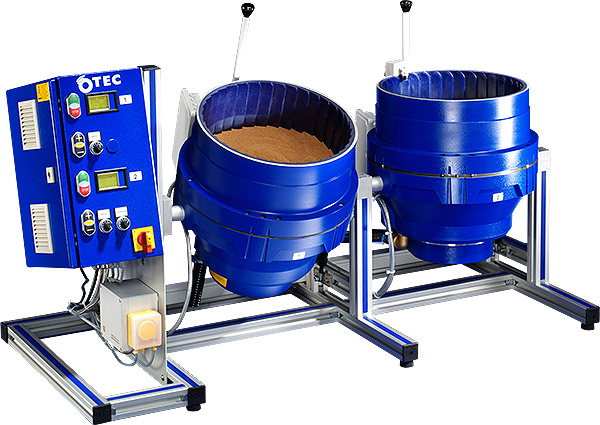
CF-T SERIES
The CF-T series is a high-performance benchtop version of the globally successful CF series with all the benefits of the CF concept. It is ideal for deburring and grinding industrial workpieces and especially suitable for finishing jewellry.
STANDARD EQUIPMENT
- High-quality gap system with ceramic rings for using extra-fine polishing granulate
- Speed control via frequency inverter
- Digital display of preset time, elapsed time, speed and error messages.
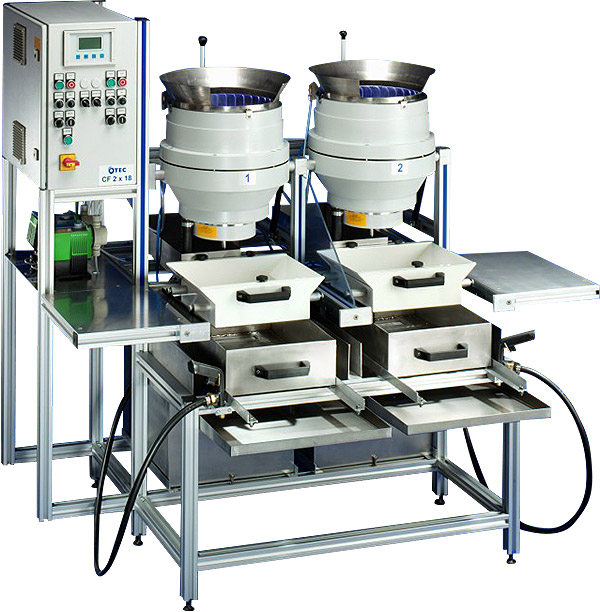
CF OIL SERIES
This series has been specifically designed for use with special grinding and polishing abrasives in combination with oil instead of a water/compound mixture. They are especially suitable for workpieces which have only a very slight degree of burring (e.g. secondary burs after grinding processes). This means there is no need for cleaning or anti-corrosion surface treatment, etc…
STANDARD EQUIPMENT
- Process drum with hot moulded PU lining
- Aluminium profile chassis – easy to add on optional equipment
- Speed control via freqency inverter
- PLC touch screen control unit / 2D control unit (for jewelry applications) with digital display of processing time, speed, rinse cycle, dosing and other key process parameters and storage of up to 75 different finishing programs.
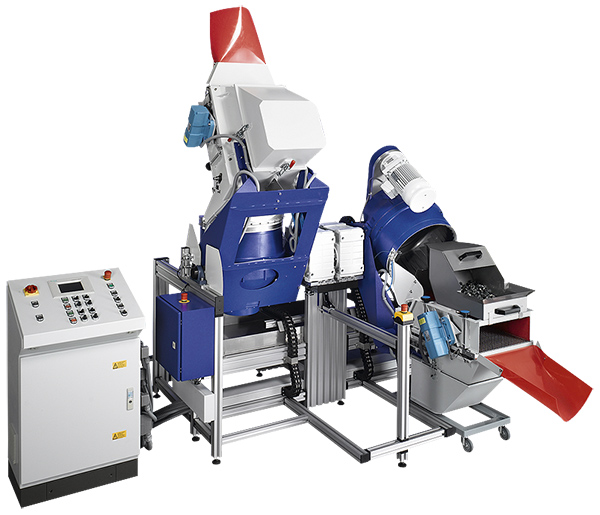
CF MR SERIES
Flange-mounted separator unit with vibration motors and automatic process medium return. When the process drum is emptied, the workpieces are automatically separated from the medium. The abrasive medium is automatically returned when the drum swngs back. The medium can easily be changed by using an intercheangeable reservoir. An ingenious mechanical system provides quick and tool-free screen change.
STANDARD EQUIPMENT
- Separation by means of vidbration motor
- Quick screen change
- Siemens S7/200 control unit
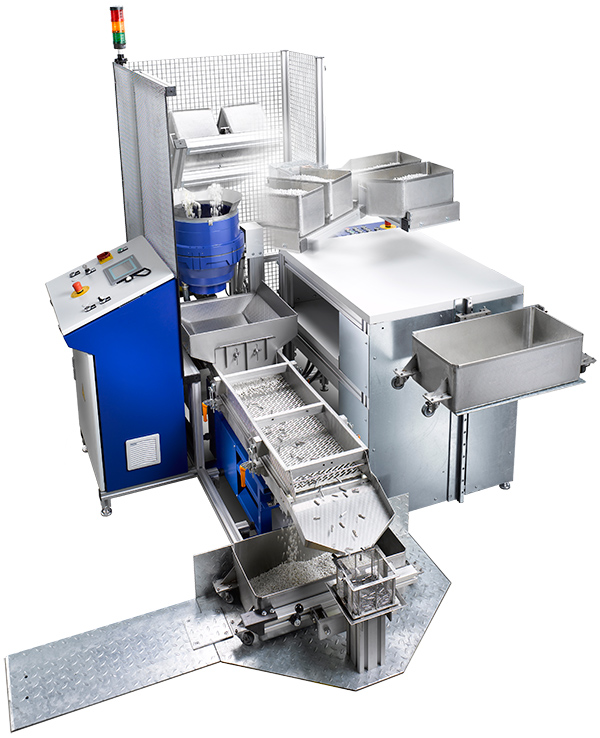
CF 18 OIL SERIES SEMI-AUTOMATIC
This unit was integrated into the customer’s work flow, put into operation and tested. The customer’s requirements were met in full.
STANDARD EQUIPMENT
- Screens and bach container in stainless steel
- Second batch filled automatically once the first batch is finished
- Media lift makes it easier to fill the batch containers
- Once the process is complete, separation is automatic
- Uses the oil from the upstream process
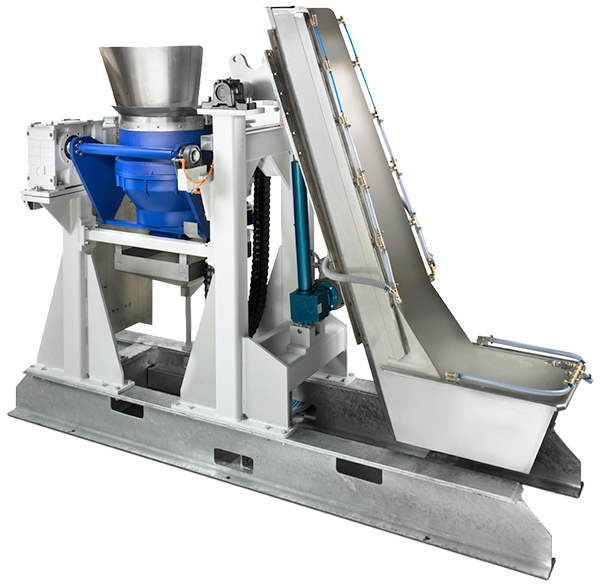
CF 50 SERIES AUTOMATIC
A CF 50 machine with zero gap system was integrated into a customer’s existing fully automatic installation, put into operation and tested. All of the customer’s requirements were fulfilled.
STANDARD EQUIPMENT
- Integrate into existing space
- Integrate into existing control system
- No mixing of workpieces
- Gentle workpiece transfer
- Automatic recycling of abrasive media
- No mixing of abrasive media
The difference between the centrifugal forces acting on the workpieces and the process medium creates a very powerful finishing effect. This can be up to 20 times more efficient than, for example, conventional vibrators. With wet finishing, a water/compound mixture flows continuously through the system, rinsing away the fine particles of debris from the finishing process. This gives the workpieces a clean and corrosion-free surface. Many years of experience have been channelled into these machines, making them very popular with customers.
CERAMIC GAP SYSTEM
With this system, the gap can be set to an accuracy of 0.05 mm since it is formed by using two ceramic rings made of SIC. this technology is best suited to dry finishing since it enables best results to be obtained by using very fine polishing granulates.
CERAMIC/POLYURETHANE GAP SYSTEM
This standard system from OTEC is suitable for the most common applications in wet finishing. The cermic/polyurethan combination prevents any workpieces from becoming lodged in the gap area, making the process very reliable and reducing maintenance requirements.
UNIQUE ZERO GAP SYSTEM!
For the wet finishing of very fine workpieces. The gap between the rotating disc and the stationary drum can be reduced to zero. This enables very fine grain abrasive media such as quartz to be used and prevents any workpieces from becoming lodged in the gap.
TESTS NOT PROMISES
Let us prove how good our technology is. We will be happy to put the performance of OTEC technology and the CF series to the test. We will give you detailed advice and develop a finishing concept tailored to your needs and formulate the best grinding and polishing media for your application. In addition, we offer to finish a sample workpiece for you with no obligation and to provide you wth a process log documentng all key process parameters.